GUOWANG T-106B DIE-CUTTER WITH BLANKING
A new generation of T106B has a number of new technologies and systems that will help you to improve efficiency significantly and bring competitive advantage. It has the function of automatic separation of pressing boards with two sets of waste clearing. Regardless of how the layout of the printing and the use of what kind of substrate, can be used in high-speed operation to clear the waste, as well as to ensure the orderly separation of finished products. The stripping chase adopts pneumatic automatic lifting up and down, and is provided with a standard quick-lock device and a center-line positioning function, which can make the preparation operation more quick and convenient. The front and back operation interfaces use 19 inches LED touch screens, making the most complex settings become simple and intuitive, to maximize the efficiency of the equipment.
- High quality MABEG feeder, 4 pick-up suckers and 4 forward suckers, ensure stable and fast feeding.
- Pre-loading device to feed paper without stopping the machine, maximum stack height 1600mm.
- Pre-loading tracks help the operator push paper stack to feeding position accurately and conveniently.
- Side lays can be adjusted to fit different paper.
- Paper transferred to the front lay will slow down to ensure accurate positioning.
- Transferring plate is stainless steel imported from Germany to make the paper conveying smooth and fast.
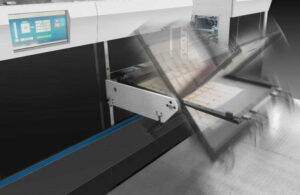
- Japanese Fuji servo motor, to achieve the precision and stable control of die cutting pressure.
- Makes accurate adjustment through the 19 inch touch screen with precision to 0.01mm.
- Die cutting chase and plate are locked by Japanese SMC pneumatic cylinder, to avoid the upper and lower chases out of position and operating losses caused by human factors.
- Die cutting chase adopts the center-line device for fast positioning , so that the operator don’t need to consider the left-right position of the die board.
- Die cutting boards of non-standard size can also be installed by using auxiliary tools to facilitate applicability of customers’ cutting boards from different models .
- Gripper bar, of special aluminum alloy , the surface after oxidation treatment, provided by Japan Komori, adopts double-cam opening method to release the paper during running. It can reduce the inertia of paper to collect the thin paper in order easily.
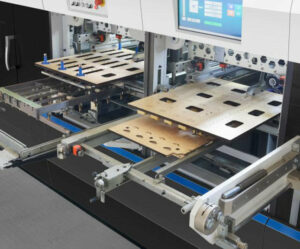
- Adopts pneumatic lifting function.
- Adopts center-line positioning and quick-lock device for stripping board .
- Stripping chase position memorization.
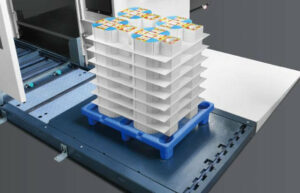
- non-stop delivery unit.
- Automatic paper pile transfer, transfer working pallet to delivery unit, then place the empty pallet to wait for proceeding, can reduce manual intervention and ensures non-stop delivery.
Maximum paper size | 1060*760 | mm |
Minimum paper size | 400*350 | mm |
Maximum cutting size | 1060*745 | mm |
Maximum Die-cutting plate size | 1075*765 | mm |
Die-cutting plate thickness | 4+1 | mm |
Cutting rule height | 23.8 | mm |
First die-cutting rule | 13 | mm |
Gripper margin | 7-17 | mm |
Cardboard spec | 90-2000 | gsm |
Cardboard thickness | 0.1-3 | mm |
Cirrugated spec | ≤4 | mm |
Maximum working pressure | 350 | t |
Maximum die-cutting speed | 7500 | S/H |
Feeding board height (incl. pallet) | 1800 | mm |
Non-stop feeding height(incl. pallet) | 1300 | mm |
Delivery height(incl. pallet) | 1400 | mm |
Main motor power | 18 | kw |
Whole machine power | 24 | kw |
Voltage | 600V 60Hz 3ph | v |
Cable thickness | 16 | mm² |
Air pressure requirement | 6-8 | bar |
Air consumption | 300 | L/Min |